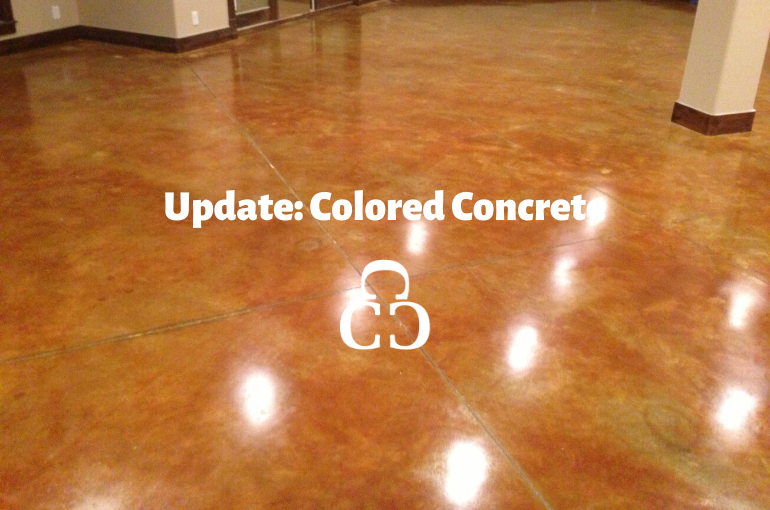
One of the benefits of using concrete is that you have so many options to choose from when it comes to aesthetic and design choices. This can be nice because most business owners want their space to stand out against the competition. Creating a good environment for your guests and customers is a great way to be sure that people keep coming back to enjoy your space!
An awesome way that some owners choose to advertise their business is with an overlay. This allows for the logo of the business or words to show through the polish and sealant to give a unique look. Another way to get a unique look is by adding color to your concrete floors. This could help blend in with the design you already have, or it could be used to offset different elements of your room. Either way, choosing a unique flooring is a great way to make your space more special.
Types of color
There’s colored concrete and then there’s stained, dyed, or painted concrete. The difference is that with colored concrete iron oxide color pigment is added to the concrete when it is being mixed. The color particles are so small that they completely coat the larger concrete particles. The color outcome is greatly affected by the ratio of water and cement. Making sure that the amount of water added is exact is very important to have a consistent color. If there is too much water added the color will appear lighter than desired.
Slump control admixtures can be used to eliminate hassle on the job site with added water. Water isn’t only an issue when it’s in the mixture, water on the surface of the concrete during the finishing process can impact the color, too. To prevent this problem, if the surface of the concrete is drying out too fast use a surface evaporative control agent instead of water. You can find these at most distributors. Surface evaporative control agents are extremely helpful when laying all types of decorative concrete.
Another factor with colored concrete is how gray cement impacts the final color. The color added to the mix needs to overpower the natural gray color of concrete. The color added mixes with the natural gray concrete to form the final color. This explains why all colored concrete that is mixed with gray cement is with deeper earth like tones. The only good way to have a lighter appearance when using color mixed with concrete is to buy white cement, which isn’t cheap. Another thing to consider is that not all gray cement is the same shade. Some gray cement can be a battleship gray and other cement may be close to white.
Choosing a color
You can control the color better by using the same cement brand from the same distributor for the entire project. Never switch distributors in the middle of a project because it can cause probelms with colored concrete. Ensure that your distributor knows that you are using the cement for a colored project and have them check to make sure you are getting cement from the same lot number. Water to cement ratio is the biggest problem when it comes to colored concrete, but problems with cement is the next biggest issue when it comes to color problems with colored concrete.
Curing colored concrete properly is also a factor to consider. Without proper curing, you will have color inconsistencies that could lead to having to remove and re-pour the concrete. Which no one wants to do. To prevent this, use a colored curing compound or colorwax that matches. Some manufacturers even already have a colored curing compound on their samples or color cards. You want to make sure that the curing compound is blush resistant and non yellowing when using colored concrete.
Lastly, the other factors that can cause problems with colored concrete are sub-base preparation, placement, finish and maintenance. It is important to maintain a consistent color with concrete when working on a larger project. One idea is to add bands of different texture or color to help make any inconsistencies unnoticeable. It can also be a good idea to use dry shake color hardeners, this can also make the color appear more uniform with fewer inconsistencies. If you are looking to add a polished concrete flooring to your space, contact Custom Concrete Creations to get started on your space transformation!